The Very Exciting Minaal Quality Control Process
ANSI. ASQ. AQL.
If those acronyms are familiar to you, our sympathies.
If they're not – time to get excited!
Since sitting in a small fluorescent-lit room looking at bags for a week straight tends to generate thoughts along the lines of "I would like someone else to share this delightful experience", here's a sneak peek into our Quality Control process.

The Basix
We spelt 'basics' with an x because we're writing about Quality Control and we need every tiny drop of excitement we can get.
Jokes! QC is actually pretty interesting.
The basics are what you probably imagine: we make an order, our manufacturing partner places orders for materials and components, then once everything arrives, it's Time To Stitch.
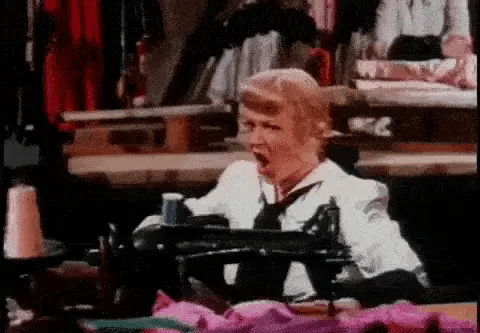
As soon as production begins, QC supervision swings into action.
Inline QC Inspection
'Inline' is the fancy industry term for 'during production'.
There are two parts to Inline: manufacturer's Quality Assurance, and external QC.
Our manufacturing partner has its own in-house Quality Assurance team; this team manages the quality of the workmanship, using the standards we've set ("extremely hardcore, bro") before production.
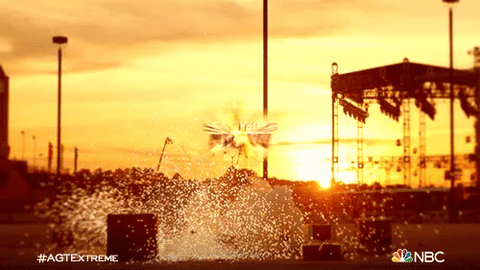
We love working with that team, but of course it helps to have another set of eyes, and for that reason we also do our own Inline QC.
The point of Inline QA and QC is to catch any issues early, before they get repeated into thousands and thousands of bags, in a scenario that can only be described as 'nightmarish' and 'potentially business-destroying'.
Pre-shipment QC Inspection
After production and thus inline inspections are complete, we move on to Pre-shipment Inspections.
This is a different process: instead of inspecting individual units as they come off the production floor, we randomly select boxes of finished and packed units to inspect.

The standard we use for this – and for Inline – is called ANSI/ASQ Z1.4.
Fun fact: sometimes people ask us whether our gear is 'military-spec' (also known as 'extremely hardcore'). There's no simple answer to that, but the short version is basically "yes" and the longer version is "did you know ANSI/ASQ Z1.4 itself actually started out as a military spec, MIL-STD-105E?"
Anyway, defects are divided into three categories under the AQL (Acceptable Quality Limit): Critical, Major, and Minor. Each shipment is allowed 0 Critical, 1.5 (...?! don't ask) Major, and 4 Minor.
To give you an idea of what we consider a 'major' defect, here's a line of stitching we'd never dream of letting onto the ship and into your hands:

Under these strict limits, we test literally hundreds of points on each unit – does each zipper slide smoothly? Are the dimensions accurate? Does the shoulder harness hold well beyond the weight it'll need to? – before giving it the green light.
The end result is a 60+ page report, per inspection, before anything heads out the door and in your general direction.
If a very sneaky defect does somehow manage to make it through to you, we still take 100% responsibility under our warranty. We own the quality of the gear from the first stitch.
And that's (an extremely condensed version of) it!
We know we'll be absolutely swamped by your questions below about the QC process, so please form an orderly queue.
1 comment
Great article on QC. I love my Carry On 3.0. So many amazing features and it has never failed me. Thank you!
———
Minaal replied:
Thanks James! Glad to hear we didn’t put you to sleep with the acronym soup :)